- SIEMENS Gearmotor
- NORD Industrial Gear Unit
- LENZE Gearmotor
- NORD Gearmotor
- SEW Planetary Gear Unit
- SEW Industrial Gear Unit
- SEW Gearmotor
- BONFIGLIOLI Precision Planetary Gearbox and Gearmotor
- BONFIGLIOLI Inverters and Servo drives
- BONFIGLIOLI Industrial Gear Unit
- BONFIGLIOLI Gearmotor
- FLENDER Coupling
- FLENDER Gear Unit
01
BIPEX S Backlash free Coupling high performance
Benefits
BIPEX-S couplings are suitable for mounting horizontally, vertically or in any desired position. The coupling parts can be arranged as required on the shaft ends to be connected.
The coupling can be axially plugged in.
The cam ring is pretensioned and is therefore assembled without backlash. The cams attached to the cam ring allow the coupling to compensate shaft misalignment and also provide electrical isolation since they prevent contact between the two hub parts.
BIPEX-S couplings are fail-safe. When the cam ring is worn, the claws of the coupling hubs provide for fail-safe operation.
Available in 4 different Shore hardness grades, the cam rings allow to select the optimum degree of rigidity for any application.
Application
BIPEX-S couplings within the standard catalog range are available in 10 sizes with torque ratings ranging from 0.5 to 655 Nm. The coupling is suitable for ambient temperatures of between -30 °C and +90 °C. Cam rings with alternative hardness grades can be supplied for ambient temperatures down to -50 °C or up to +120 °C.
BIPEX-S couplings are ideal for use in servo drives, linear axes or rotary encoders of the type typically deployed in machine tools, packaging machines or printing presses.
Design and configurations
BIPEX-S couplings each comprise two hub parts connected by a cam ring made of polyurethane (PU).
The couplings can be axially plugged in during assembly.
The hubs can be coupled to the shafts by many different methods including set screws, key joint, slotted clamping hubs, half-shell hubs, clamping hubs or expanding hubs.
BIPEX-S couplings are positive-locking and torsionally flexible thanks to the polyurethane cam ring. Misalignment between the connected shafts deforms the cam ring.
Coupling materials
Hubs Up to size 38 aluminum
Sizes 42 and 48 steel
Cam ring PU 80 ShoreA -50 °C to +80 °C
PU 92 ShoreA -40 °C to +90 °C
PU 98 ShoreA -30 °C to +90 °C
(standard ring)
PU 64 ShoreD -50 °C to +120 °C
The coupling types can be combined from the available range of hub versions and different elastomer grades.
Hub versions
Hub Description
N Hub with set screw
G Slotted clamping hub
C Slotted clamping hub, compact
H Half-shell clamping hub
K Clamping hub with external taper
S Expanding hub
The N version has a keyway as standard. Versions G, C and H are optionally available with keyway.
The fitting tolerance of the coupled shaft ends should be g6 or h7.
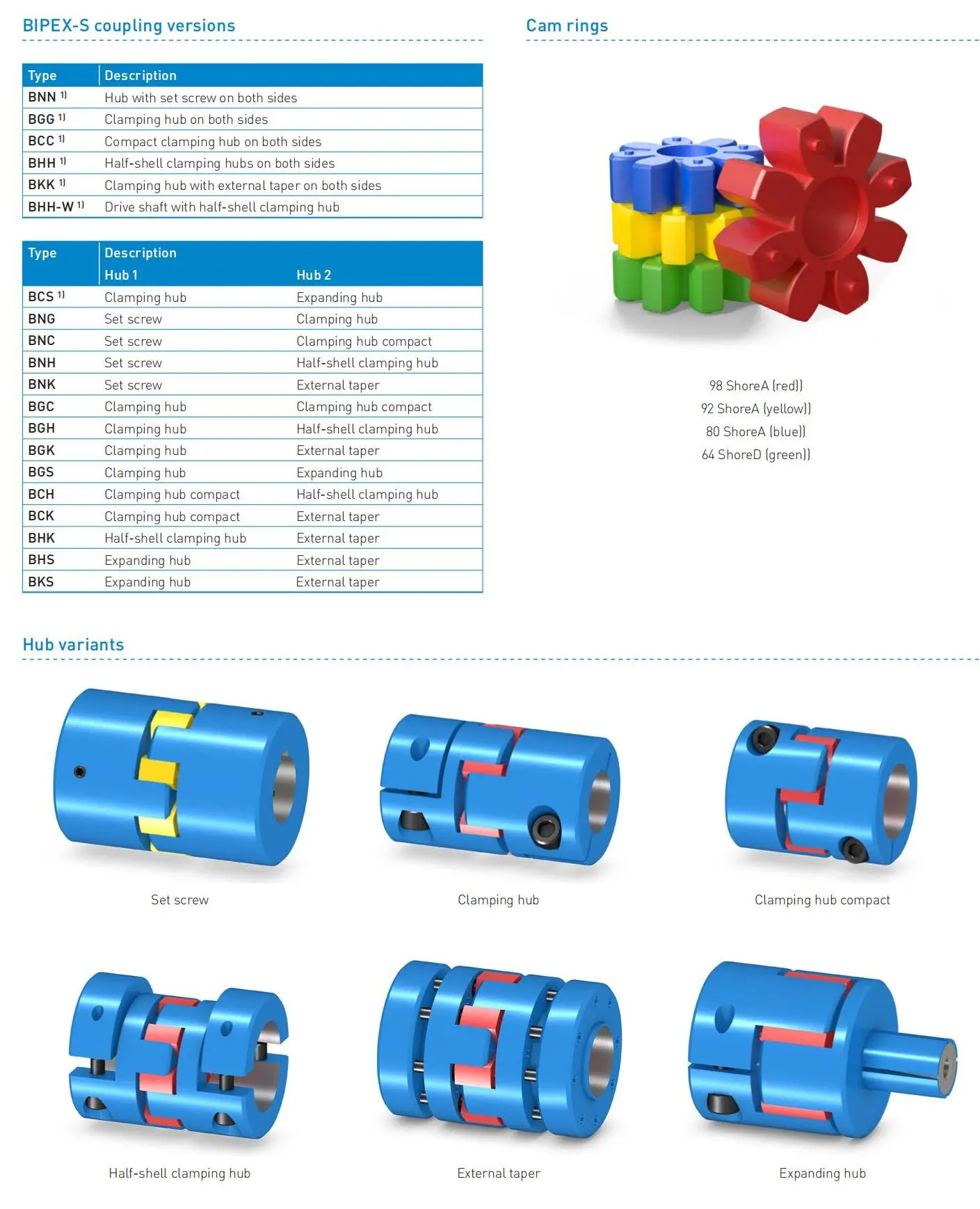
Preliminary dimensioning
Dimensioning according to torque
The coupling must be dimensioned such that the rated torque of the drive including service factors does not exceed the rated torque of the coupling:
TKN ≥ TN ⋅ FB ⋅ FT
Torque characteristic Service factor FB
Uniform 1.25
Non uniform 1.5
Rough 2
In order to increase the torsional rigidity and therefore minimize the torsional backlash, it is possible to apply significantly higher service factors for main spindle or positioning drives.
Temperature range Temperature factor FT
-30 °C to +30 °C 1
to +60 °C 1.4
to +80 °C 1.8
to +100 °C 2
to +120 °C 2.8
Note:
Please note the permissible temperature ranges of different cam rings.
Starts per hour Startup factor FA
< 125 1
125 to 250 1.3
250 to 500 1.6
500 to 1000 1.8
> 1000 2
Preliminary dimensioningChecking the peak torques
The coupling size selected during the preliminary dimensioning process must also be suitable with respect to peak torques at the drive and load ends:
Checking the maximum speed
For all load situations nKmax > nmax
Checking the permitted shaft misalignment
The actual shaft misalignment must be less than the permitted shaft misalignment for all load situations.
Checking the shaft-hub connection
In the case of clamping connections without feather key, it must be ensured that the transmissible torque of the hub connection is greater than the peak torque at the coupling.
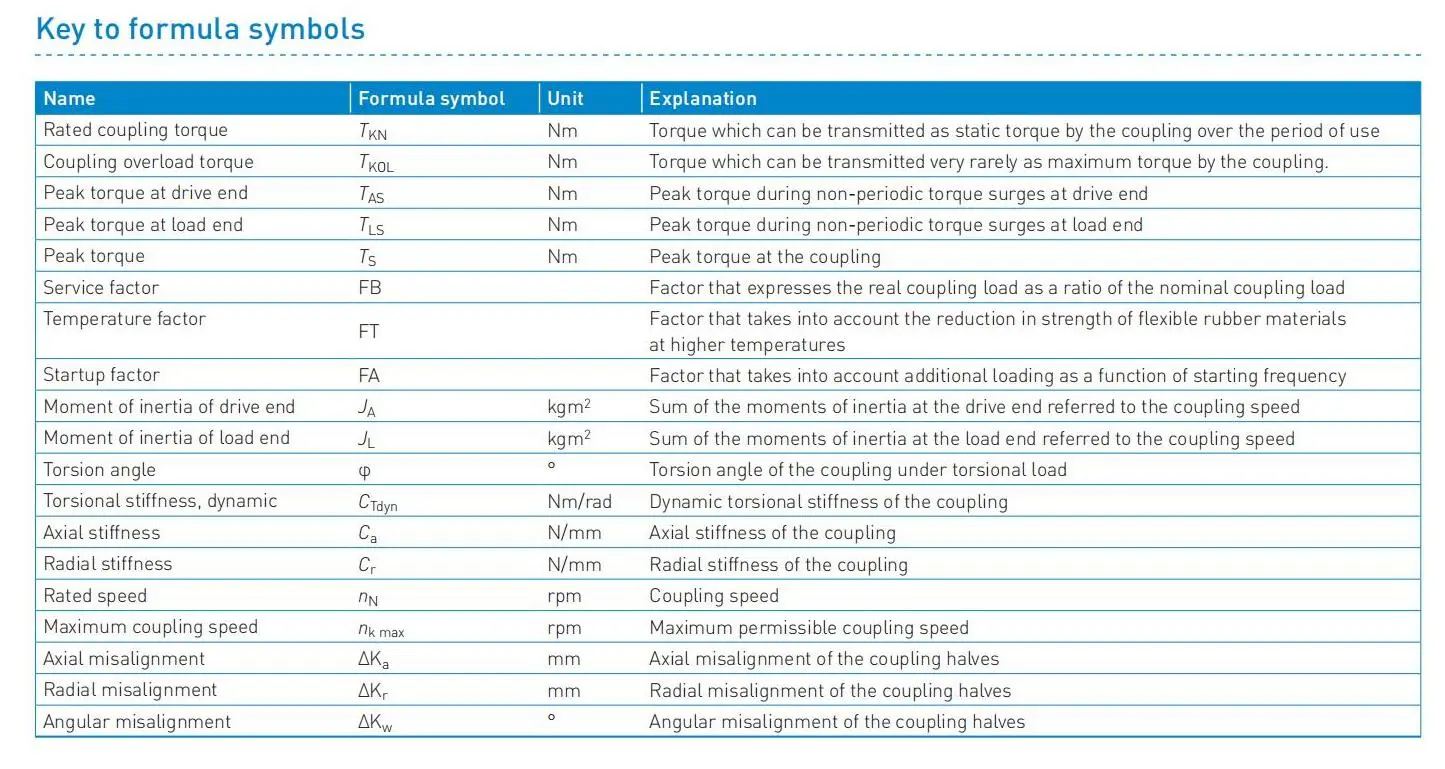
Technical information
Torsional stiffness and damping
The values stated in the table apply to a capacity utilization of 50 %, an excitation amplitude of 10 % TKN with a frequency of 10 Hz and an ambient temperature of 20 °C.
The dynamic torsional stiffness is load-dependent and increases in proportion to capacity utilization.
The relative damping coefficient is
ψ = 0,8 for 98, 92 and 80 ShoreA
ψ = 0,75 for 64 ShoreD.
TKOL is the torque which can be transmitted very rarely as maximum torque by the coupling.
Zulässiger Wellenversatz
The permitted shaft misalignments ΔKa, ΔKr and ΔKware maximum values and must not occur simultaneously.
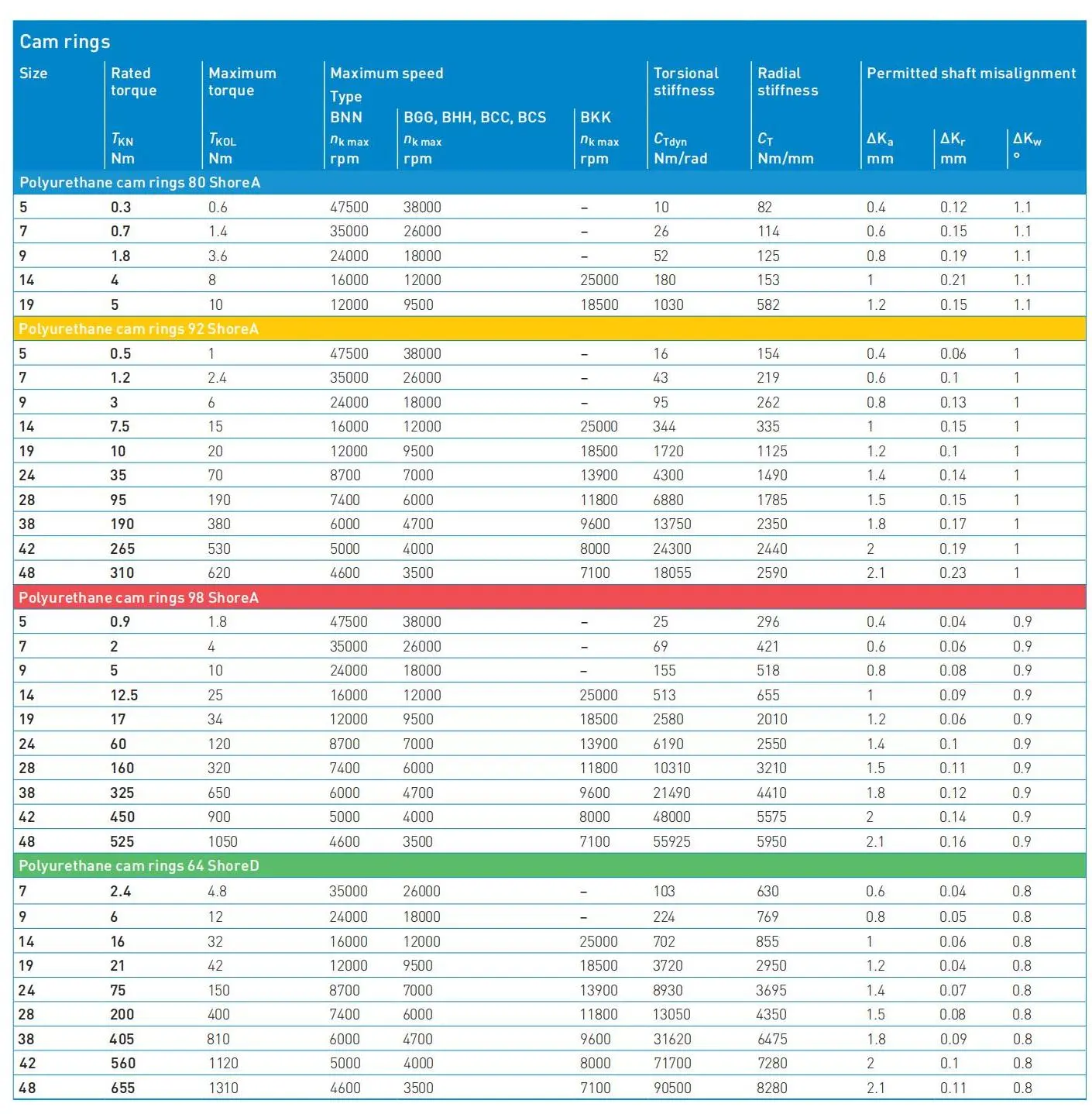
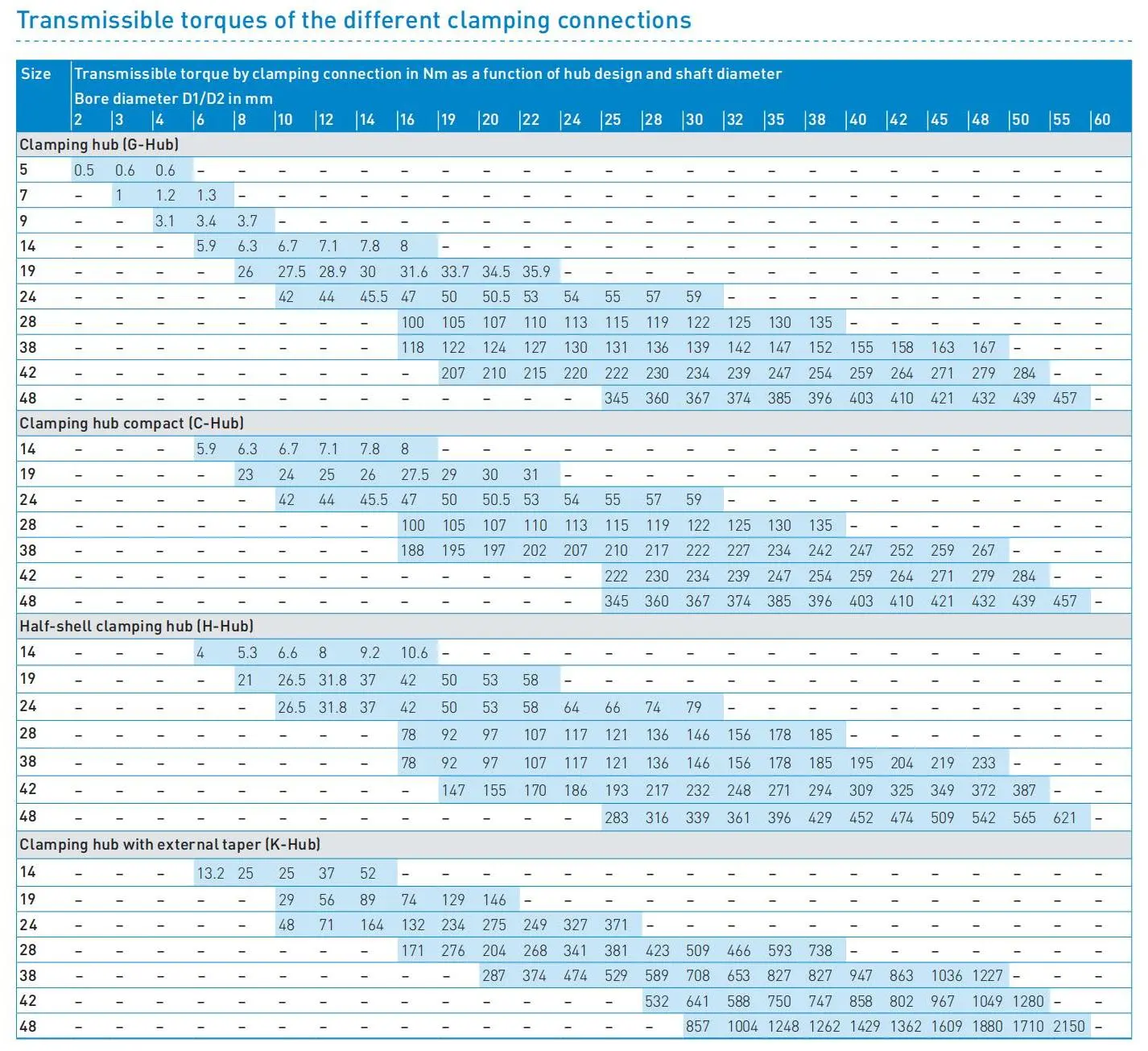